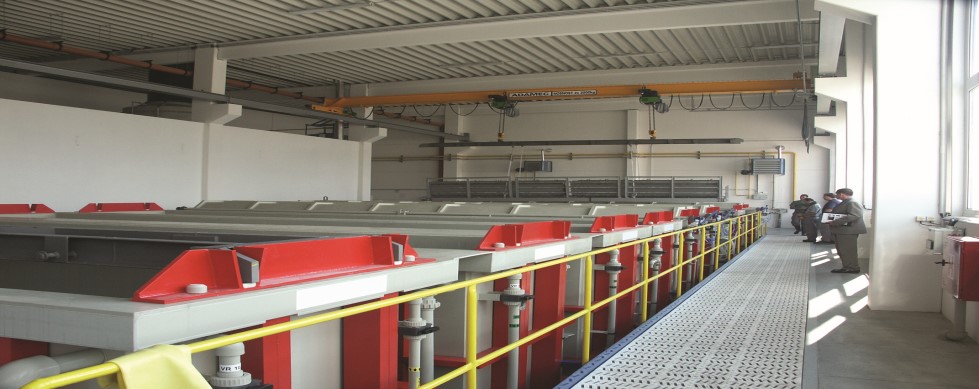
Pickle Passivation
Maximising the life of our stainless steel products
Pickle Passivation
Pickle Passivation is a two-phase process.
Pickling removes both the bluish high temperature oxide film and the chromium depleted layer and is achieved by placing the components in a pickling bath containing a mixture of nitric acid and hydrofluoric acid. The second phase is passivation and in many ways is similar to the pickling process. During this process the components are placed in a bath containing only nitric acid. This treatment strengthens the passive layer and also removes any iron impurities that may have become embedded in the surface of the stainless steel during the manufacturing process.To achieve the highest quality for our products we use pickle passivation to remove both the bluish high temperature oxide film and any other impurities from the manufacturing process. The treatment renews the protective passive layer to ensure maximum lifetime expectancy for our stainless steel drainage products.
This treatment is important where mechanical cleaning of the components has taken place with the use of wire brushes, grinding wheels and files where iron particles from other materials may contaminate the stainless steel surface.
Electropolishing
Electropolishing is ideal for producing a uniform, highly reflective lustre with an extremely smooth finish even on the most complex product contours. This is a well proven method of polishing and is achieved by an electro-chemical process which is essentially the reverse of electroplating.
The components are immersed in a bath of electrolyte containing phosphoric acid where the components become the anode of a direct current electrical circuit. The process is characterised by the selective attack on the surface of the components whereby upstanding roughnesses are preferentially dissolved and will yield a progressively smoother, brighter surface.
For pharmaceutical and food processing industries, bacterial resistance is considerably improved by the electropolishing process.
Certain gratings within the ACO Building Drainage range are electropolished as standard. All stainless steel products can be electropolished if required to special order.
What do ACO do?
All ACO Building Drainage products are subjected to specialised treatment to ensure the material retains the maximum resistance to corrosion.
The chemical processing methods used in the ACO Building Drainage process are pickle passivation and electropolishing. ACO resources include the largest pickle passivation plant in Europe.
The standard ACO Building Drainage manufacturing process uses pickle passivation to restore products to their full optimum corrosion resistant state without damaging the surface finish. This is considered the best method for cleaning welded joints. This ensures the products we supply are produced in such a way as to maximise their life and provide best value.
What is important with Stainless steel?
A stainless steel finish should appear clean, smooth and faultless. This is obvious when the steel is used for such purposes demanding stringent hygiene or decorative trim applications, but a fine surface finish is also crucial in respect to its corrosion resistant properties.
The corrosion resistance properties of stainless steel are achieved by the spontaneous formation of a very thin chromium-rich oxide layer over the surface of the material.
Unfortunately, surface defects and imperfections introduced during the manufacturing process may drastically disturb the self healing process of the passive layer and subsequently reduce the corrosion resistance of the material.
In the manufacturing process it is welding that creates the greatest challenge to corrosion resistance.
What happens if Stainless steel is left untreated?
After welding stainless steel, a bluish high temperature oxide film can be seen which has substantially inferior corrosion protection properties compared to the original passive layer. Immediately beneath this blue oxide film is a thin layer of chromium depleted metal which makes the metal surface susceptible to corrosion. Post weld treatment is, therefore, very important to restore the corrosion protection properties and is effectively achieved by removing the blue high temperature oxide film and chromium depleted layer to restore the surface of the material.
This ‘cleaning’ is essentially a controlled corrosion process using chemicals, this will restore not only its original corrosion resistance performance but also the high quality aesthetics.
The single most important property of stainless steels and the reason for their existence and widespread use, is their natural corrosion resistance. In spite of their name, stainless steels can both ‘stain’ and corrode if used incorrectly.
The reason for the good corrosion properties is due to the formation of a very thin, invisible oxide film that forms on the surface of the material in oxidising environments such as the atmosphere and water.