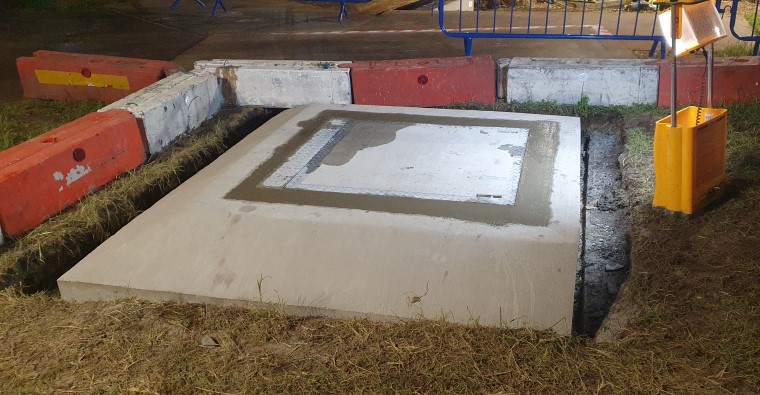
Securing Safety: ACO’s Bespoke Escape Hatch is a Runway Success
When an outdoor emergency escape hatch needed replacing at Heathrow airport, it was vital the solution could be installed quickly to minimise disruptions to air traffic as much as possible. With no escaping the difficulties inherent to projects carried out at the world’s fourth busiest airport, the contractors reached out to ACO to help them hatch a plan.
Time for an upgrade
The escape hatch in question served a plant room below the south runway and, as the one previously in place was reaching the end of its useable life, it needed updating. Intended for emergency use should there be a serious problem in the plant room, the existing hatch featured a grill near ground level which left the inside of the plant room vulnerable to frequent rainwater ingress. Due in large part to the age and outdoor location of the site, the previous hatch had become difficult to open so something more useable was required.
Safety needed to be front of mind – the new hatch needed to be openable with one hand and allow someone on the inside to override the outside locking system so that in emergency situations workers could escape quickly. These operational requirements had to be tempered with the fact that airports are high-security environments so any risk of unauthorised entry via the hatch had to be reduced to practically zero.
The escape hatch installation was contracted to Design Build International (DBI) and headed up by Construction Manager Kelvin Sumner. DBI had just four nights to break out the existing escape hatch, install reinforcements, pour concrete, and install the new hatch.
Flight path pressure
Working at an airport meant there were several constraints specific to the site with security and safety requirements meaning that transport to and from the site took multiple layers of approvals and permits. This restriction meant planning was vital because a forgotten tool or unexpected change would mean having to wait until a member of security was available before making the round-trip to pick up any additional items.
Most of the installation work had to happen at night to avoid interrupting airplane landings and take-offs. This also meant that DBI had to be very strict about leaving the site by 4:30am each day.
Along with the airport-specific restrictions, the fact that the project impacted an escape route meant that scaffolding had to be assembled to provide an adequate escape route during the day. At night, when DBI undertook the project, work couldn’t begin until the scaffolding had been disassembled. Available time was similarly reduced at the end of their shifts as they had to have each phase of the job completed early enough in the morning so that scaffolding could then be reassembled for the temporary escape route.
Bespoke solution
Given the restrictions around the time available for this project, it was vital that the installation of the new hatch went smoothly. Knowing that the escape hatch would need to be fully bespoke and made to very strict standards, Kelvin brought ACO on board. Having worked with ACO on a previous project, Kelvin knew the manufacturer’s ability to offer unique solutions as well as their speed at delivering them.
ACO supplied the fully bespoke escape hatch which suited the project as it was designed with ease of installation in mind. All aspects of the operational specification were met allowing the cover, once installed, to be opened from above and below ground level. Not only this but, thanks to its gas springs and one-handed quick release mechanism, it is easier – and therefore safer – to use in an emergency. When used from inside the hatch, the mechanism can override the lock outside, ensuring security while enabling quick escapes.
While there is no expectation for vehicles or aeroplanes to go over the hatch, to account for that unlikely (but still possible) event, the hatch has been specified to BS EN 124 load class F 900 meaning it will be able to safely withstand the force of even the heaviest vehicles. The load class and external locks combined with the water-tight seal means the escape hatch will not allow unwanted ingress of any kind.
Advantages of ACO
To support DBI with the constraints of working at an airport, ACO provided a detailed installation guide. The escape hatch was itself designed to be swift and uncomplicated to install and this meant that, when the night came to carry out the installation, the process was completed smoothly and in good time. The entire project, from removal of the existing escape hatch to installing ACO’s bespoke replacement, was completed within the four-night timeframe.
Kelvin Sumner, Construction Manager at DBI said: “Working with such tight timescales every night made for a pretty tense job but thankfully, when it came to installing the new escape hatch, we could essentially just place it in the right spot and fix it down. The guide ACO gave us was thorough enough that we knew exactly what was needed for a quick install and the escape hatch is very easy to use. Between the design elements, the fast turnaround with the supply, and the installation guide, I don’t think there’s anything else ACO could have done to make this part of the job go better.”
Kevin Bohea, Managing Director at ACO Building Drainage said: “We’re really glad the hatch is now safely in place and that the installation went without a hitch. We do our best to understand the pressures that contractors face and mitigate that at every stage, from the initial ideas for solutions we come up with, to design, to additional after-sales support. DBI has been a great partner to work with and it’s great to know that we were able to make the job a little easier.”